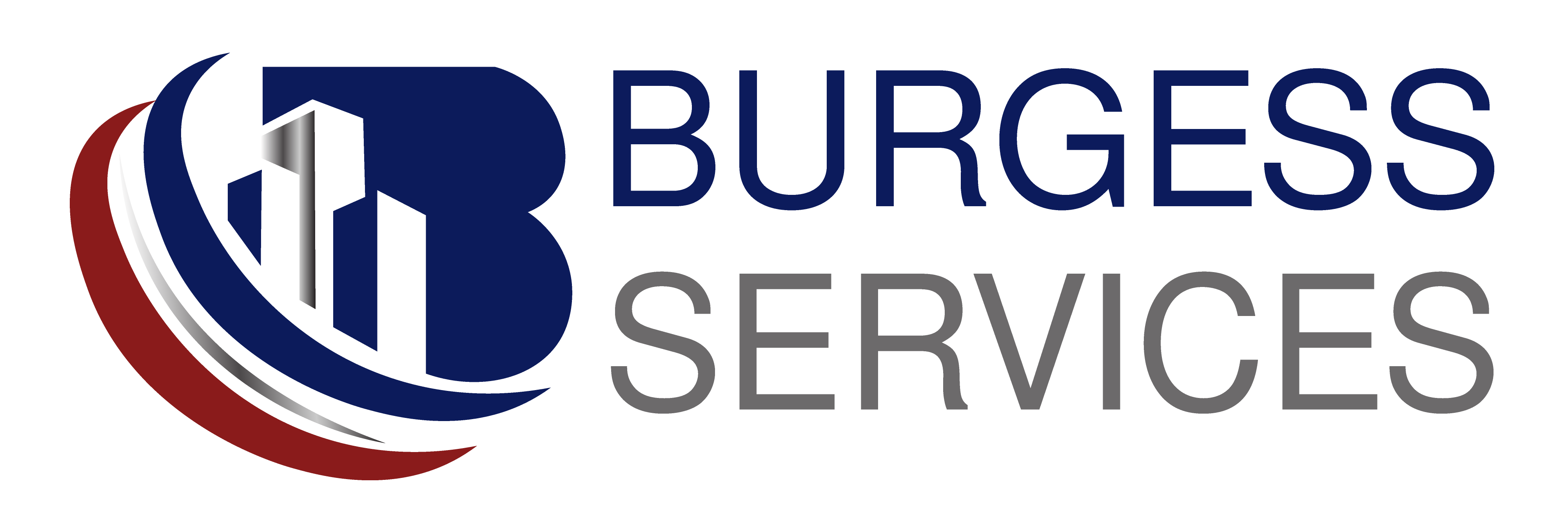
Application details
Email: info@burgessservices.com
Phone: 7202387837
City: Denver
Zip code: 80222
Job description
Burgess Services is a 50-year-old privately owned construction management firm based in Denver, specializing in large commercial public projects. This position oversees and implements the organization's health, safety, and environmental policies and procedures to ensure compliance with regulatory requirements and to promote a safe and healthy workplace.
Requirements:
Qualifications/Experience:
•Must hold a Board of Certified Safety Professionals CSP with at least 4 years of full-time relevant construction safety and health experience; or
•Must hold a Board of Certified Safety Professionals ASP, GSP, or SMS with at least 6 years of full-time relevant construction safety and health experience; or
•Must hold a Board of Certified Safety Professionals CHST or OHST with at least 8 years of full-time relevant construction safety and health experience
•Must have completed the OSHA 500 course for construction within the last 24 months, remaining current for the duration of the project.
•Must provide proof of non-expired completion of a Red Cross or approved equal for Cardio–Pulmonary Resuscitation (CPR), First Aid, and Automated External Defibrillation (AED).
•Must provide proof of completion of FMCSA compliant 2-hour drug and alcohol reasonable suspicion supervisory training.
•Must have knowledge of and ability to fulfill contractor safety representative’s responsibilities set forth in this Manual and the Contractor’s CSPP where applicable.
•Computer literacy is required.
•To perform this job successfully, an individual should have knowledge of Microsoft Office suite including word processing software, delivery software, and basic Excel spreadsheet software.
•Must be willing to travel to project locations in Denver Metro region.
Work conditions:
Language Ability:
Ability to read, analyze, and interpret common scientific and technical journals, financial reports, and legal documents. Ability to respond to common inquiries or complaints from customers, regulatory agencies, or members of the business community. Ability to write speeches and articles for publication that conform to prescribed style and format. Ability to effectively present plans and specifications information to top management, public groups, and/or boards of directors.
Reasoning Ability:
Ability to define problems, collect data, establish facts, and draw valid conclusions. Ability to interpret an extensive variety of technical instructions in mathematical or diagram form and deal with several abstract and concrete variables.
Certificates and Licenses:
•Certified Safety Professionals CSP; or
•Certified Safety Professionals ASP, GSP, or SMS; or
•Certified Safety Professionals CHST or OHST
Work Environment:
While performing the duties of this job, the employee is frequently exposed to wet or humid conditions (non-weather); work near moving mechanical parts; work in high, precarious places; fumes or airborne particles; toxic or caustic chemicals; outdoor weather conditions; extreme cold (non-weather); extreme heat (non- weather) and risk of electrical shock.
The noise level in the work environment is usually loud on the jobsites.
Physical Demands:
While performing the duties of this job, the employee is frequently required to stand; walk; use hands to finger, handle, or feel; reach with hands and arms; climb or balance; stoop, kneel, crouch, or crawl and talk or hear. The employee is occasionally required to sit for long periods of time. The employee must regularly lift and /or move up to 100 pounds and occasionally lift and/or move more than 100 pounds. Specific vision abilities required by this job include Close vision, Distance vision, Color vision, Peripheral vision, Depth perception and Ability to adjust focus. The employee is regularly required to use a computer for long periods of time.
To perform this job successfully, an individual must be able to perform each essential duty satisfactorily. The requirements listed are representative of some of the knowledge, skill, and/or ability required. Reasonable accommodations may be made to enable individuals with disabilities to perform the essential functions.
Responsibilities:
Essential Duties and Responsibilities include, but are not limited to the following, as other duties may be assigned:
•Conduct safety orientation sessions for all on-site workers and representatives.
•Inform employees of their safety rights and responsibilities per regulations and the manual.
•Participate in weekly safety meetings (toolbox talks).
•Help field supervisors with meetings when requested.
•Hold monthly safety meetings for supervisors.
•Engage in Job Hazard Analysis and Pre-Task Planning, assisting subcontractors with their safety programs.
•Teach employees special safety procedures as required by OSHA and the manual.
•Assess employees' adherence to safety rules and standards.
•Provide necessary regulatory training for all site employees.
•Conduct training for emergency action plans.
•Maintain and retain OSHA, state, federal, company, and project-specific documents for the project duration or as legally required.
•Investigate incidents and near misses, perform causal analysis, and distribute corrective actions within 72 hours.
•Complete daily inspection reports and audits.
•Maintain training documentation.
•Keep drug test results for all project employees and respond to drug test audits within 24 hours.
•Respond to other safety documentation audit requests within 72 hours.
•Authorized to take immediate corrective action, including stopping work; deemed a "competent person" by OSHA.
•Possess organizational freedom to enforce safety and health programs for Contractor and Subcontractor.
•Implement, maintain, and update safety policies and procedures as required.
•Interpret and enforce site-specific safety policies and procedures.
•Model proper safety behavior.
•Ensure Contractor management enacts disciplinary action for unsafe behavior.
•Ensure adequate first aid supplies.
•Lead and facilitate all incident investigations, complete reports, and submit to DEN within 72 hours.
•Coordinate and facilitate injury treatment for all on-site workers, provide modified duty within restrictions, and check in with injured employees weekly.
•Inform DEN ROCIP Safety Team and Project Manager immediately of all injuries after ensuring treatment and securing the site.
•Provide injured employees with the Designated Medical Provider list before non-emergency or follow-up treatment, ensuring they choose an authorized facility and return the signed form.
•If an employee denies treatment, they must indicate so on the Designated Medical Provider Form, sign, date, and return it.
•File the first report of injury with the insurance carrier within 12 hours of any employee seeking medical care, including subcontractor injuries.
•Inform DEN ROCIP Safety Team and Project Manager of any current or potential safety issues.
•Maintain proactive, professional, and collaborative safety partnership with DEN.
•Review all safety submittals to ensure they meet contract requirements before submission to DEN, ensuring submissions come through the General Contractor's document control software.
•Conduct daily safety inspections of work areas and provide results to DEN ROCIP Safety Team upon request, possibly using specified forms or programs.
•Address all safety issues logged in BIM360 within 24 hours.
•Compile and send safety statistical information to the DEN ROCIP Safety Team.
•Participate in weekly construction meetings with DEN.
•Attend quarterly safety meetings scheduled by the DEN ROCIP Safety Team.
About company
0-20 employees
Denver